電動工具を扱う際は、事故・怪我の無い様、十分過ぎるほど注意してください。全ては
自己責任です。
丸鋸インデックス
丸鋸スライド台
丸鋸の改良
日立工機 C6UVH
決定版丸鋸スライド台
スライド・ベース更新
マキタ LS0813FL
スライド丸鋸用ジグ
スライド丸鋸でホゾ取り
丸鋸スライド台
木工を始めていろいろ木材の切断をしているうちに、切断そのものより、その準備作業に
かなり時間を
取られることが分かりました。
・切断線の罫書き
・切断ガイドのセット
どちらもいい加減にするとそれなりの出来上がりになってしまいます。また、引き出しの部材など
同じサイズのものを複数切断する場合も、それぞれの長さ、幅などが微妙に違ってしまいます。
卓上スライド丸鋸があれば一挙に解決なのですが、縦引きが出来ない、専用の作業所が無いので、
形状が大きく、重量がある卓上スライド丸鋸は避けたい。また刃が上を向いている丸鋸台は恐怖感!があります。
そしてそれにもまして何も考えずに他のものに飛びつく事にも抵抗があって、このスライド台を作ってみました。
ホームセンターではプラスチック製の同じような台が売られていますが、あえて考えて作る事も楽しみの内です。
約600×400mmのスクラップの21mmベニヤ板に50mm角の角材、そして厚さ3mmのアルミアングルが
主な材料です。アルミアングルには丸鋸のすべりを良くするため、エンビのモール(アングル状)を
両面テープで貼り付けてあります。アルミアングルは切り始めにぐらつかないよう、手前に長くしています。
アルミアングルは最初、左側も等辺アングルでしたが、刃を目いっぱい出すとモーターの位置が下がり、
このアルミアングルにぶっかってしまうので、左側は不等辺アングルです。
次の組み立てで調整しますので台板自身の直線・直角は余り気にしなくていいと思います。
<組み立て>
1.最初に手前の角材を台にネジ止めし、次に一方のアルミアングルを角材に対して直角になるよう取り付け、
そして丸鋸がぐらつきなくスライドするようもう1本のアングルを取り付けます。(プラスチックモールは乗せるだけ)
2.先端側の角材に2本のアルミアングルを、やはり丸鋸がスムースにスライドする幅で取り付けます。
3.先端の角材をクランプで固定し、不要な木材を実際に切断し、先端の角材の位置を左右に動かし、
切り口が納得のいく!直角になるよう微調整を繰り返します。
OKならば角材を木ねじで台に固定し、そしてプラスチックモールを両面テープでアルミアングルに固定します。
スライド台の材料費は数千円で済みました。その他トグルクランプはYahooのオークションで入手、
アルミのTスロットとTボルトはピクチャーレールのもので、入手先はリンクのページを見てください。
手持ちの丸鋸は165mmですので、刃を目いっぱい出すと、台に数ミリ切り込む感じになります。
私が使ったアルミアングルではスライドした時丸鋸の刃カバーがうまく開かず、切断する時はカバーを
開いておかないと駄目でした。従ってその状態での丸鋸の扱いは細心の注意確認をします。
これは今後の要改良点です。
これで、材料に切断マークをつけさえすれば、あるいは手前側の角材か台にストッパーをつければ
同じ長さの切断が簡単に出来るようになりました。また角度切りも簡単です(45度のケガキ線)。
切断は、台からはみ出したガイド部分に丸鋸を乗せ、回転させてから進めます。
切断の際は材料をしっかり固定しないとキックバックなどで思わぬ怪我をする危険があります。
材料をしっかり固定する、これはどの場合でも鉄則です。
小さな材料の固定、これが意外と難しいのですが、ホームセンターで手に入る金属パーツで作ってみました。
材料は台に6mmの鬼目ナットを埋め込み(台の裏側から)、3mm厚鉄ステー金具を緩やかに曲げたもの、
そして6mmの蝶ボルトです。木材を傷つけないためにはステー金具にゴム、プラスチック等で
カバーしたほうが良いようです。これらの材料は安いものですから、鬼目ナットを台のあちこちに埋め込んで
おけば、無理してTスロットを使わなくても十分実用的だと思います。
2002年5月
丸鋸の改良
使用している丸鋸は165mmのマキタ M560です。安さにひかれて購入したのですが、
実際に使用して
いろいろ問題があることが分かりました。
パワー、重量などは平均的?、ベースは鉄板ですが角度切りが出来るようにベースに対して
刃の角度が
変えられるようになっています。ベースとモーター部の固定は、角度ゲージがある先端はしっかりしている
のですが、ハンドル側はこの切断角度を変えるためにりベットで止めてあるだけです。
その為、切断する際、力の入れ具合で刃の角度が変わってしまうことが分かりました。
角材を切断すると切り始めと切り終わりで微妙に切り口の角度が違います。
価格の高いアルミベース、造作丸鋸などはこの構造がしっかりしていてぐらつきが少ないようです。
次々と買い換えるわけにも行きませんので、リベットをドリルでサラって取り外し、代わりに6mmの
ボルト・ナットでしっかり止めるようにしました。
刃を傾けて切断する事は今のところほとんどありませんが、その場合はこちらのナットもゆるめて調整します。
こうしても鉄板のベース自体の剛性不足は残るようですが、切り口は多少ましになりました。
May 2002
日立工機 C6UVH
M560のベースの安定度が悪くて正確に切断するのが難しいので、インターネットで通販をしている工具店の
秋のセールを機に購入しました。アルミベース、レーザーマーカーつきの造作鋸です。ブレードは72Pが
ついていました。
これと「カット師」という商品名の2mの切断定規(エッジがステンレスで処理されています)を使って、
1間程度の長さまでは、途中の体の移動の時さえ気をつければ、ジョインターをかけなくてもまあまあの
切り口に切断できるようです。
OCT 2002
決定版丸鋸スライド台
昨年作成した丸鋸スライド台ですが、パワーツールの中では最も使用頻度が高く、その間に上から物を
落としたり、誤って踏みつけたりして直角が怪しくなってしまい、山勘?で狂いを補正しながら使うように
なってしまいました。またガイドのアルミのアングルも強度不足で、そろそろ次の手立てを考える必要に
迫られてきました。
手っ取り早いのは卓上スライド丸鋸ですが、かさばる形状をしていて、また工具店で、モデルによっては
スライドを一番引き出した状態では結構ぶれがあるという話を聞いたりで、今ひとつ踏み切れません。
行き着くところはテーブルソーでしょうが、大きさ・重量があり、スライドレールなどの重装備のものでないと
本来の精度や使いやすさは望めない、こんなものを引っ張り出したり、収納したり出来るわけが無く、
カタログを横目にため息です。
現実的に考えた結果、幾分意地もあったかもしれませんが・・・、結局はスライド台に落ち着きました。
スライド機構はFAに使われているリニアガイド/リニアスライドがベストですが、めちゃくちゃ高価で、
またこのような宙ぶらりんの構造ではガイドレールの構造・強度が心配です。
そこでリニアシャフト+リニアブッシュを使うことにしました。リニアブッシュはオークションで安く出ていて
16個衝動買い!したTHK製 20φ両端シール付未使用品のストックがありました。これは5列のボールで
(5個ではありません)で保持する頼もしい構造をしています。
リニアシャフト 20φ 800mm長 両端加工なし 2本とシャフトを固定するためのセットカラー4個は
TSK(竹内精工)からWEB通販で購入しました。ほんとに少量オーダーですが、個人取引業者として登録し、
商社を通すより安く入手出来たようです。ここでリニアブッシュも入手できます。(WEBで登録しないと
商品カタログを閲覧できません。)
規格品に下の画像のようなシャフトホルダーがありますが、高さが足りないので今回は使用しませんでした。
本来はリニアブッシュのホルダも同程度の精度のものを使いたいところですが、外径は32φで
市販品には無く、特注したら目が飛び出るような価格になりそうですし、ハウジング付のリニアブッシュも
高価なので諦めました。
一番の問題は穴あけ・取り付けなどどう頑張ってもコンマ何ミリの精度は絶対!出せないだろうという
点です。下手をするとスライドしないという最悪の事態もありえます。
それなら破れかぶれで遊びをもたせ、だましながら組立したらどうだろうか? という、機械屋さんが聞いたら
目を剥くようないいかげんな方法でやってみることにしました。
居直ってみると使えそうな材料は簡単に手に入ります。リニアブッシュのホルダーは水道パイプ用ですし、
丸鋸のマウントベースは300mm長の建材の帯金を2つに切断したものです。
簡単なものですから、画像からお分かりと思いますが、
・台は24ミリ厚のベニヤ合板 900×600mm
・シャフトホルダーは木材(米松)です。手押しカンナと自動カンナで仕上げました。
・シャフト4箇所の穴明けはボール盤にフェンス、ストップを取り付けて、台からの高さ(68mm)、間隔(190mm)が
極力同じになるように努めました。絶対精度ではなく、2対の加工が同じであれば良い という考えです。
調整後セットカラーできっちり固定します。
・リニアブッシュのホルダーと丸鋸マウントベースの穴は大体の位置に開け、丸棒やすりで横長に広げて
組み立て時に調整できるようにしました。金属の穴開けは、センターポンチでマーキングしても、
ほんのちょっとのずれでドリルの刃が逃げてしまい難しいです。
・このリニアブッシュのホルダーには斜めに2つ穴を開け、ブッシュのロックを兼ねて、セルフタップねじで
横方向に微調が出来るようにしました。
全てを仮組みして、スムースにスライドするように、また切口が直角になるよう試行錯誤しながら
徐々にネジを締め上げていきました。
よりどころはリニアシャフトとリニアブッシュ自体の精度で、これがスムースに動くなら、木工用には
十分な精度は確保されるはずという思い込みです(笑)
丸鋸のベース自体に剛性があるので、六角ボルト・ナットで取り付けるとより全体の剛性が増したようです。
またシャフトのベースに丸ゴムを取り付けて、スライド両端での衝撃を和らげています。
最初スライドがスムースに動くかどうかばかりに気をとられてしまっていたので、下の画像のように
切り口にブレードの跡が丸く残ってしまいました。
そこで下左の画像のように、スコヤで丸鋸ベースとリニアシャフトのアラインメントと、丸鋸ベースの高さ
などを調整しなおしました。コンマ数ミリには追い込めたと思います。
切り口は下右の画像のようにきれいになりました。
この構造の難点は、(リニアブッシュの外径)/2+αの分、切り込み深さが減ってしまうことです。
実際には165mmの丸鋸では 55-16=約39mm 、190mmでは 68-16=約50mm位です。
実際の切断時は、ブリードが1ミリほど台に切り込むぐらいにします。台に残った切り込み跡は
切断マーカーにもなっています。
最大切り込み深さでの切断幅は、おおよそ(レールの長さ)-(丸鋸ベースの長さ+α)となりますが
190mmの造作丸鋸で約350mm確保できますし、材料の下に当て木をすれば500mm程度までいけます。
このシャフトの径であれば欲張ってシャフトを900mm長以上にして切断幅をかせいでも、剛性に問題は
なさそうに思われます。
丸鋸は日立工機の電子造作丸鋸 C7UVHで、このように丸鋸のベースと材料が離れてしまう場合は
レーザー・マーカーが切断線合わせに便利で、ブレードを傾ける斜め切りの場合も切断箇所が
はっきり分かりますが、これは晴天の屋外では見にくくなってしまいます。
そのためもあってフェンスを取り付けました。四隅を直角出しした角材を、8φのボルトと台に埋め込んだ
鬼目ナットで90度、45度に固定するようにし、Tスロットでストッパーをつけられるようにしています。
材料押えは、バークランプのハンドル部分を取り外して流用しました。しばらく使ってみると他にも
あれやこれや改良点が出てくるかもしれません。
使用感はリニアシャフト+ブッシュならではで、スムースに楽々と切断出来ます。シャフトに付着した切屑が
リニアブッシュの中に入り込むのが心配でしたが、右上の画像のように、ブッシュのシールがうまく
そぎ取ってくれるようです。後は、集塵機のホースと接続できるように考えるつもりです。
注意点は、ブレードカバーが開きっぱなしになることですが、下向きなので手を突っ込まない限り心配は
ないと思います。切断する材料をクランプなどでしっかり固定する点はこのスライド台に限りません。
材料費はリニアブッシュが@200円×4、リニアシャフト2本とセットカラー4個が約7000円、後は
ホームセンターで購入したもろもろで1000円程度でしょうか。
もし精密な金属加工が出来る知り合いでもいて、リニアブッシュのホルダーと丸鋸マウントベースを
一体構造に出来ると申し分のないものになると思います。ある金属材料を扱っている業者に厚さ20mmの
アルミで加工の見積りを取ったところ、材料込みで@4500円ぐらいでした。
2003 March
スライド・ベース更新
大田区の金属材料屋 五十嵐商工にリニアブッシュ・ホルダーの加工を依頼していたのが
出来上がってきました。幅40mm 厚さ20mmのA5052 アルミ平角棒を加工したものです。
リニアブッシュ32mm径穴、それをロックする6mmタップ、丸鋸を乗せるアングル取り付け穴/5mmタップ
がついています。
精度が上がったため、リニアシャフトのアラインメントが正確でないとスライドしないという
事態になり、もう一度全ての調整を行い完成したのが下の画像です。
見た目ががっちりしただけでなく、不安定要素が無くなってほぼ完璧なものになったと思います。
2003 APR.
マキタ LS0813FL
リニア・シャフト、リニア・ブッシュなどを使用して別の実験をすることになり、これを購入しました。
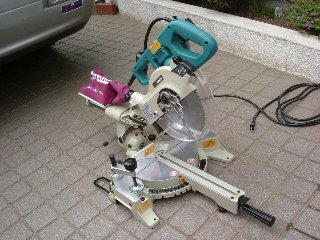
2003 Oct.
スライド丸鋸を使用する場面が多くなっています。横切りは問題ないのですが、細い材料をさらに縦に切りたい場合、なかなかいい方法を思いつきませんでした。しっかり固定されていないと危険であるばかりでなく、断面が焦げたり、ブレードの跡がついてしまったりします。また市販のクランプではうまく固定できなかったり、スライドの邪魔になったりして使えませんでした。
最近旋盤等の本を読んでいる中で、金属加工の際の材料のクランプ方法がヒントになり、下のようなジグを製作しました。
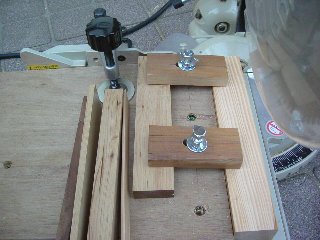
厚ベニヤのベースの右上角は正確に直角にしておき、いろいろな長さの材料を最適に固定できるよう、4ケ所に8ミリの埋め込みナットをつけています。材料の押さえ板は10×4センチ程度の硬い木に穴を明け、8ミリの長ボルトに蝶ナット・ワッシャーを組み合わせています。
ポイントは押さえ板を出来るだけ水平にすることで、材料の傾きや、振動によるずれを防ぐ点です。そのため、画像左のようにいろいろな厚みのスペーサーを用意して、押さえ板の左側に挟むようにします。
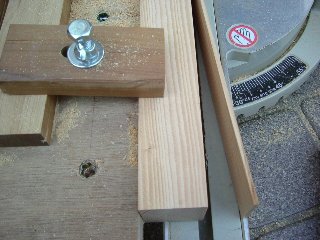
画像は5センチほどの幅の角材から。さらに厚さ3ミリほどの薄板を切り出しているところです。材料を軽く叩いてジグに密着するように固定、正確かつ安全に切断が出来ました。切断する材料の幅がもっと小さい場合は、押さえ板ごと切断するようにすれば確実ですし、また簡単に作ることができます。厚板の切断では押さえ板の数を増やせばもっと確実です。
スライド幅までの切断なら、スライド鋸で十分こなせます。
*24ミリ厚ですので、切断時にベースを手で押さえれば問題ありませんでしたが、材料をクランプした時にベースの前部が浮き上がってしまうようでしたら、前部に穴を開けてLボルトなどでスライド丸鋸のベースに固定するといっそう堅固になります。
材料をベースに乗せてもいいですし、いろんな発展形が考えられますね。
2004 June
縦方向はバンドソーで切りますが、横方向はスライド丸鋸の方が効率的です。切り込み深さを調整する黒いつまみがありますが、右画像のような高さが80ミリほどある材料の場合は、そのままでは切り込みが深すぎます。そこで左画像のように小さな板を置いてストッパーにすると、この画像のように15ミリの切り込みもできるようになりました。上のFさまのテーブルは結合部は全てホゾにしていますが、簡単に加工できました。
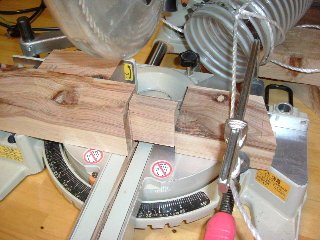
2004 Aug.